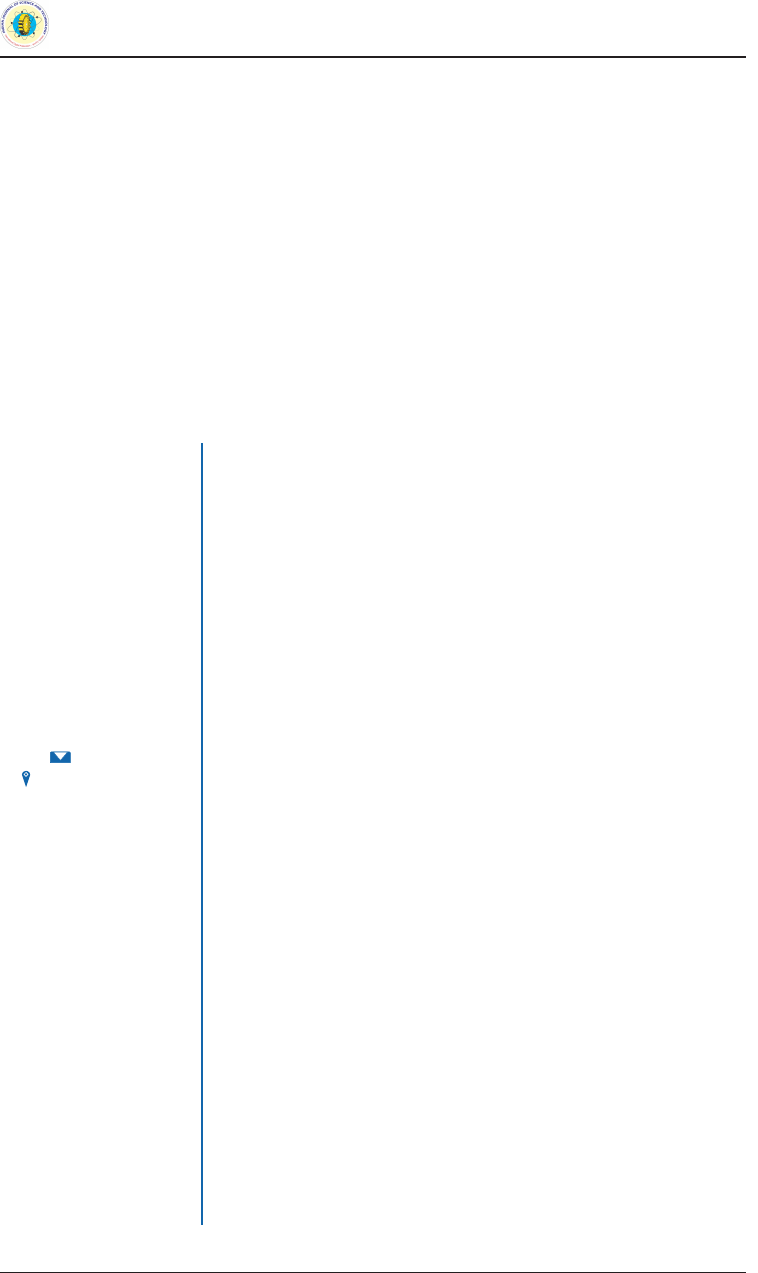
ISSN (Print) : 0974-6846
ISSN (Online) : 0974-5645
INDIAN JOURNAL OF SCIENCE AND TECHNOLOGY
February 2020, Vol 13(05), 502 – 518
DOI: 10.17485/ijst/2020/v13i05/145593,
© 2020 The Author(s). This is an open access article distributed under the terms of the Creative Commons Attribution License, which permits unrestricted use, distribution, and reproduction in any medium, provided the
original author and source are credited.
Equipment Sizing and Method for the
Application of Exhaust Gas Waste Heat to Food
Crops Drying Using a Hot Air Tray Dryer
C. Ononogbo
1,
*, O.C. Nwufo
2
, C.A. Okoronkwo
2
, N.V. Ogueke
2
,
J.O. Igbokwe
2
and E.E. Anyanwu
2
1
Department of Mechanical Engineering Technology, Imo State Polytechnic,
Umuagwo, Owerri, Imo State, Nigeria
2
Department of Mechanical Engineering, Federal University of Technology, Imo State,
Nigeria
Abstract
Objectives: Equipment sizing and method of utilizing exhaust gas
waste heat for food crops drying are presented. Methods/ndings:
The sizing of the components of the equipment was achieved using
known design principles. The system uses an axial ow turbine and
a heat exchanger to harness the energy of the exhaust gas of a diesel
engine generator. A 250 kVA generator with measured exhaust gas
ow rate and temperature of 44.5 m
3
/min and 382.7 °C was selected
for this work. The purpose of the recovered energy is for the drying
of food crops. An arduino platform was used to control the operation
of the components of the dryer. The drying chamber consists of
three trays whose calculated total volume per batch is 0.0463 m
3
.
Weight losses across the trays, drying air temperature and humidity
in the chamber are monitored by sensors. The test rig of the sized
and fabricated equipment is currently undergoing extensive
experimentation. Preliminary investigation of the dryer showed
that the drying air in the chamber initially at the temperature and
humidity of 31ºC and 71.2% was heated to 88ºC and 22.3% when
the dryer operated without load for 45 min at an air speed of 2.0 m/s.
Application: After cooling and maintaining the drying chamber
averagely at 59ºC, each tray was loaded with 400 g of the grains of
freshly harvested maize. The dryer was allowed to run for 30 min
and the results obtained showed weight losses of 127.81 g, 118.36
g, and 116.91 g for the grains in trays 1, 2, and 3, respectively. The
application of this energy recovery system to the drying of food
products, would help to save a considerable amount of primary fuel
which is considered a viable means of cost saving and amelioration
of environmental degradation.
Keywords: Waste Heat Recovery, Drying, Global Warming,
Environment, Cost Saving, Food Quality.
Article Type: Article
Article Citation: Ononogbo C,
Nwufo OC, Okoronkwo CA, Ogueke NV,
Igbokwe JO, Anyanwu EE. Equipment
sizing and method for the application
of exhaust gas waste heat to food crops
drying using a hot air tray dryer. Indian
Journal of Science and Technology. 2020;
13(05), 502-518. DOI: 10.17485/ijst/2020/
v013i05/145593
Received date: June 29, 2019
Accepted date: October 18, 2019
*Author for correspondence: C.
Ononogbo
@
petermaryco@yahoo.
com Department of Mechanical
Engineering Technology, Imo State
Polytechnic, Umuagwo, Owerri, Imo
State, Nigeria